In a general way, we specialize in precision casting technology and die casting molding. In precision casting technology. A technology that uses wax samples as intermediates in the product casting process. Therefore, the technology is also known in the industry known as Lost Wax.
Molded die casting technology is specifically used for casting metal and alloy products for low flow, typically under 1000 ° C, such as Mg alloy, Zn alloy, aluminum And aluminum alloy (Al). These products are often used in home appliances, motor vehicles, moto and auto.
In terms of materials used in the casting process, we cast the product with the main materials being metal, including most common metals and alloys in the market. The most frequently used metals and alloys include low melting point (Tm <1000 ° C) such as magnesium alloy (Mg alloys), aluminum alloys, aluminum alloys and aluminum alloys. (Al & Al alloys), which are commonly used in die casting molding technology. Metals and alloys with high melting point (Tm> 1000 ° C) are cast through precision casting technology with flowing wax form. Metals and alloys with high flow temperatures include, (1) ordinary steels such as CT3, (2) common carbon steels (AISI 10xxx, 11xxx, 12xxx, and 13xxx) that are incapable of heat treatment, (3) High alloyed steels (AISI 3xxxx, 4xxxx, 52xxx, 6xxxx, etc.) with heat treatment capability, (4) tool steel AISI Grades: A, D, H, F, L, M , (5) stainless steel of various types (AISI 201, 304, 316, 430, 440), (6) stainless steel for casting industry for chemical production And prefiltration (CF3, CF8, CF7M, CF8M, CN7M, and CN7MS), (7) or super inox types (AISI Types 310, 904L, Carpenter Cb-3, Incoloy 800) And specialize in such industries as thermal power, fertilizer production, paper technology, (8) white liver and gray liver for machining and engraving machines; (9) nickel and nickel alloys (International Nickel Institute, Inconel, Incoloy, Monel 400); (10) Ti (Ti) and Ti alloys (Ti alloys); (12) Zirconium alloy (Zr 702 & 703) and (13) tantalum alloy (KBI-40) in the ethanol industry, etc.
Basically, our casting process is set up and implemented in a scientific way and is arranged in a dimensional way, in which each single piece of goods and sewing is done sequentially to ensure The quality assurance and control is carried out in a convenient, accurate, and rigorous way, without being overlooked, while the test data are dissolved and kept in a proper place for 3 years. From production, to extract when necessary and draw experience in improving product quality, reduce the percentage of unsatisfactory products with the criterion of not more than 5% of the input rate > 95%).
In the molding process, In terms of mold preparation, there are two options for customers to choose: (1) Customers themselves provide molds for us or (2) We mold molds for customers at a cost. Calculate the outside cost of casting. With a molded casting product, our molding process starts, completes, and delivers finished products up to 100% of the standard quality requested by the customer for a period of no more than 30 days. Customers have some time to inspect and verify product quality, then transfer the cost of casting to us.
The market is a dynamic and constantly changing environment. However, our foundry costs are set up in a stable, long-term, market-based manner with a standard unit of time of at least 6 months or 1 year to help peace of mind in The process of commercial cooperation with us. We will notify our customers at least 30 days prior to any change in our pricing or trade standards.
In terms of reporting unit prices to customers, in a standard way, we set product prices based on the cost of molding that we perform, but not on the cost of raw materials. Products. This fee will be charged to the customer based on the actual price of the raw materials at the time of quotation, excluding any shipping costs to our foundry. Our foundry costs, as such, are standardized and covered primarily for the customer based on the cost of molding the finished product and are included in the unit price on the finished 1kg cast. This unit price is adjusted (plus), when the product weighs less than 1kg, due to the labor cost to use when manufacturing. For exact molded unit price, PLEASE CONTACT OUR COMMERCIAL CONTACT (TEL: Email:), when there are single finished products
In the production process, the quality of finished products that customers demand is our top concern. We work and interact regularly with our customers in terms of order fulfillment and especially quality standards. We will use the standards of the international market frequently used as: AISI, ASTM, ASME, NACE, ASME, ISO 9001, ACI, In my Quality Control (KCS) process, I use the standard and technology with the most advanced equipment available. These devices basically have a photo as shown below :
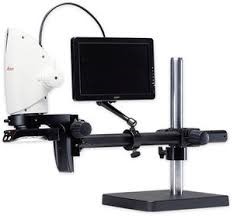 |
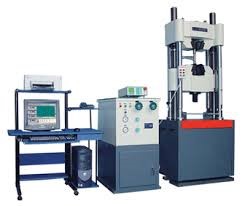 |
(1) |
(2) - (3) |
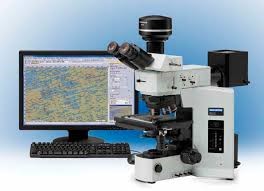 |
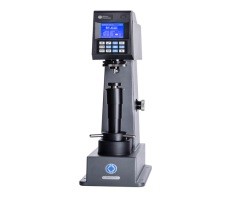 |
(4) |
(5) |
(1) Spectrophotometer – Check the metal and alloy content of the product to ensure that it meets the requirements of international customers and international standards.
(2) Metal hardness tester according to ASTM E18 and Rockwell hardness unit (HRA, HRB, HRC).
(3) Metal compression molding machine for measuring metal durability according to ASTM E8 standard
(4) Optical microscope (1x-50x) used to check the surface defects and castings.
(5) Optical microscope (50x – 1000x) to check the structure and crystal metabolism of the molded material, through or without heat treatment